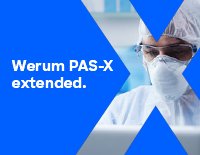
Current Good Manufacturing Practices (cGMP) refers to regulations enforced by regulatory authorities such as the U.S. Food and Drug Administration (FDA), the World Health Organization (WHO), and the European Medicines Agency (EMA) to ensure that pharmaceutical products, medical devices, and food products are consistently produced and controlled according to strict quality standards.
cGMP regulations govern every aspect of drug manufacturing, quality control, and facility operations, ensuring that products are safe, effective, and meet regulatory requirements before reaching consumers. The “current” in cGMP signifies the industry’s commitment to continuous improvement, requiring manufacturers to stay up to date with the latest advances in technology, science, and risk management.
In the pharmaceutical industry, cGMP is essential for maintaining the quality, safety, and efficacy of medicines, active pharmaceutical ingredients (APIs), and medical devices. These regulations cover every step of the drug production process, from raw material sourcing to final product distribution.
Failure to comply with cGMP regulations can lead to product recalls, regulatory actions, financial penalties, and reputational damage for pharmaceutical companies. As a result, manufacturers must ensure strict process controls, quality management, and documentation practices.
To comply with cGMP, pharmaceutical manufacturers must adhere to core quality principles that ensure the integrity of drug production. These include:
Quality management system (QMS): A structured framework that governs process controls, risk management, and quality assurance in manufacturing.
Personnel and training: Ensures that all employees involved in manufacturing, quality control, and validation receive continuous training on cGMP regulations and best practices.
Raw material and supply chain management: Strict control over raw materials, excipients, and active pharmaceutical ingredients (APIs), ensuring that only approved and tested components are used in production.
Equipment and facility maintenance: Pharmaceutical production requires validated and well-maintained equipment to prevent contamination, cross-contamination, and operational failures.
Process controls and validation: Manufacturing processes must be documented, monitored, and validated to ensure that every batch meets consistent quality standards.
Documentation and record keeping: Detailed batch records, deviation reports, and quality control data must be maintained to provide traceability and regulatory compliance.
Product testing and quality assurance: Finished pharmaceutical products undergo rigorous testing for purity, potency, stability, and sterility before market release.
Several global regulatory bodies enforce cGMP guidelines to standardize pharmaceutical quality worldwide:
Implementing cGMP offers significant advantages for manufacturers, regulators, and patients.
Ensures safe and effective products: By following strict quality control measures, manufacturers reduce the risk of contaminated, ineffective, or unsafe drugs reaching the market.
Prevents contamination and defects: Proper facility design, equipment maintenance, and process validation help minimize risks of cross-contamination and manufacturing deviations.
Regulatory compliance and market access: Pharmaceutical companies that adhere to cGMP regulations gain approval from health authorities, allowing them to distribute products globally.
Reduces recalls and legal liabilities: Compliance lowers the risk of costly recalls, regulatory warnings, and financial penalties due to manufacturing errors.
Continuous improvement and innovation: cGMP emphasizes ongoing process improvements, technological advancements, and better quality management systems.
While Good Manufacturing Practices (GMP) and Current Good Manufacturing Practices (cGMP) share the same fundamental principles, the key difference is the “current” aspect in cGMP.
GMP is a general set of quality guidelines for drug and medical device manufacturing.
cGMP incorporates the latest advancements in science and technology, requiring companies to continually update and refine processes to maintain compliance.
Regulators expect manufacturers to keep up with evolving industry standards, ensuring that production practices meet the most up-to-date safety and quality expectations.
As pharmaceutical manufacturing evolves, cGMP regulations are adapting to new challenges and technological advancements. These trends highlight the importance of adaptability, innovation, and digital transformation in maintaining cGMP compliance.
Automation and digitalization: The adoption of electronic batch records (EBR), AI-driven quality control, and cloud-based compliance management is enhancing data integrity and process efficiency.
Advanced risk management approaches: Regulators are focusing on risk-based approaches that integrate real-time monitoring, predictive analytics, and proactive quality assessments.
Sustainable manufacturing practices: As environmental regulations become stricter, pharmaceutical companies are implementing eco-friendly production methods while maintaining cGMP compliance.
Personalized medicine and flexible manufacturing: With the rise of cell and gene therapy, continuous manufacturing, and small-batch production, regulatory frameworks are evolving to accommodate new drug development models.