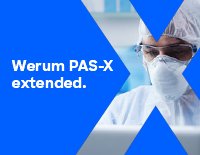
Automated Visual Inspection (AVI) is a technology-driven method used in the pharmaceutical industry to ensure product quality and safety. It employs high-resolution imaging systems and artificial intelligence (AI) to detect defects, inconsistencies, or irregularities in pharmaceutical products during manufacturing. AVI is a cornerstone of modern quality control, ensuring compliance with regulatory standards and delivering reliable, safe products to market.
Historically, pharmaceutical inspections relied on manual processes, which were prone to bias and fatigue. AVI emerged as a transformative solution, providing enhanced accuracy and scalability for modern manufacturing environments.
AVI systems integrate advanced cameras, lighting systems, and software algorithms to analyze pharmaceutical products as they move through production lines. Here’s how the process typically works:
This automated process replaces manual inspections, significantly reducing human error while improving efficiency and accuracy.
Automated Visual Inspection (AVI) systems are crucial to ensuring product quality and compliance in pharmaceutical manufacturing. These systems are highly versatile and can be used across various stages of production.
Packaging inspection: AVI systems play a vital role in verifying the integrity of packaging materials such as blister packs, vials, ampoules, and syringes. The inspection process ensures that all packaging is correctly sealed and labeled, minimizing the risk of contamination or mislabeling during the manufacturing process.
Defect detection: One of the primary uses of AVI systems is to detect defects in pharmaceutical products. This includes identifying cosmetic defects, cracks, foreign particles, and discoloration in both solid and liquid formulations. By leveraging advanced image processing, AVI systems ensure that defective products are removed from the production line before reaching the market.
Serialization and traceability: AVI systems support compliance with traceability requirements by verifying serialization data, such as unique identifiers on product labels. This ensures that products can be tracked throughout the supply chain, reducing the risk of counterfeit pharmaceuticals entering the market.
Aseptic manufacturing: In sterile environments, AVI systems help maintain contamination-free production by inspecting critical components and ensuring adherence to stringent quality control standards.
By applying AVI technology, pharmaceutical manufacturers can streamline their production processes while enhancing product quality and safety.
The adoption of AVI systems offers significant advantages for pharmaceutical manufacturers, addressing both operational efficiency and compliance requirements.
Enhanced accuracy and consistency: AVI systems utilize machine vision and artificial intelligence to identify even the smallest imperfections, ensuring consistent product quality. Unlike manual inspection, AVI systems maintain accuracy across high-speed production lines, reducing variability caused by human error.
Improved efficiency: Automating the inspection process significantly increases the throughput of the manufacturing process, enabling manufacturers to handle larger volumes of products without compromising quality. AVI systems operate in real time, ensuring immediate defect detection and minimizing downtime caused by quality issues.
Regulatory compliance: Compliance with regulatory bodies such as the FDA and EMA is a key concern for pharmaceutical manufacturers. AVI systems enhance compliance by ensuring that all products meet the required safety and quality standards. This includes adherence to serialization and labeling guidelines, as well as product integrity requirements.
Cost savings: While the initial investment in automated visual inspection systems can be substantial, the long-term cost savings are significant. AVI systems reduce waste, minimize rework, and lower labor costs associated with manual inspections. By improving overall process efficiency, they deliver a strong return on investment.
Actionable insights through data: Modern AVI systems collect and analyze data during the inspection process, offering manufacturers valuable insights into production trends and recurring defects. This data can inform improvements in production processes and help identify potential issues before they escalate.
Support for diverse pharmaceutical products: AVI systems can inspect a wide variety of pharmaceutical forms, from tablets and capsules to liquid injectables and sterile products. Their flexibility makes them suitable for both small-batch and large-scale production environments.
These benefits underscore the importance of AVI systems in maintaining high standards of quality control and operational excellence in pharmaceutical manufacturing.
While AVI offers transformative benefits, there are some challenges associated with its implementation:
High initial investment: Advanced systems require substantial upfront costs.
Integration complexities: Aligning AVI systems with existing workflows and data infrastructure can be challenging.
Training requirements: Operators and quality teams must be trained to use the technology effectively.
Despite these challenges, the long-term gains in efficiency, quality, and compliance make AVI an essential investment for forward-thinking manufacturers.
The future of AVI lies in its integration with cutting-edge technologies like deep learning and cloud-based solutions. Deep learning algorithms will enhance detection capabilities, allowing systems to identify even subtle defects. Meanwhile, cloud-based platforms will enable real-time monitoring and data sharing across production facilities, enhancing operational transparency. Additionally, innovations in intelligent packaging and sustainable manufacturing practices are expected to complement AVI systems, ensuring they remain at the forefront of pharmaceutical quality control.