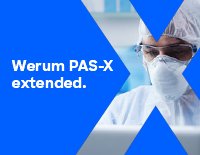
The cell & gene therapy industry (CGT) is growing at a staggering 30% CAGR and is estimated to reach $14B by 2025. At the same time, search for talent and laboratory capacity is getting harder. Thus, more and more CGT companies rely on Contract Development Manufacturing Organizations (CDMO) for manufacturing with adherence to stringent regulatory cGMP conditions.
CGT manufacturing for both autologous (patient to patient) and allogenic (donor or cell bank to patient) treatments face difficult issues such as a complex supply chain, strict traceability conditions, variability on patient and cellular level and a tight scheduling of the batch disposition process. This complexity affects quality, compliance and accountability in the entire vein-to-vein process for the critically ill patients.