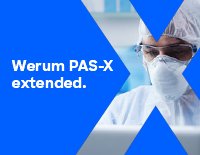
What makes a national soccer team successful? Is it the technique of the individual player or team? And most importantly, how best to compare bioprocess development to the glamor of football?
Just in time for the World Cup, the Economist magazine published a statistical review of all national football team results to parse out what effects impact the goal differential between countries. Interestingly, but perhaps unsurprisingly, up to 40% of the variation was explainable by culture, government support, and stable organization of the national football league. While 60% presumably lies within the talent and development of the team, a surprising amount of the success of a football team may be tracked not to the techniques but to the cultural and social management of the environment in which the football team plays.
Dare we compare biotechnologists to football stars? Sure, let’s have a go: first of all, because we are all at least, if not better looking on average than football stars. Secondly, because the variation in the success of bioprocess development depends on much more than having the best hardware and software systems available.
Organization of bioprocess data and data analytics is Koerber’s bread and butter. However, no matter how solid our collaborative results are, if the culture & management around bioprocess development is not sound, the results will either not be accepted or, if accepted, will not be continued in the future.
In creating a state-of-the-art bioprocess development department, culture and organization are at least as important as all hardware and software systems combined. Here are some of the key principles, from our experience in process development, that will ensure a sustainable, advanced development environment:
Comments
No comments