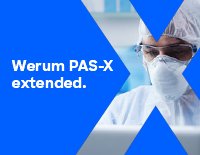
The pharmaceutical industry faces unique challenges in manufacturing and production processes – especially in times of rapid digital technology transfer. One critical process in parenteral pharmaceutical manufacturing is the visual inspection of primary packages such as syringes, vials, or ampoules. In this process, potential product defects, impurities, or contaminants must be detected in each individual product, hence the term: “100 percent inspection”.
The automatic visual inspection (AVI) is a common practice in the industry. This inspection method however brings along false reject rates (FRR), which can lead to costly re-inspections.
Ensuring reliable detection results with traditional vision tools requires at least 5 to 15 product samples per defect and configuring up to 18 cameras per machine. This process is expensive, time-consuming and error-prone, costing the pharmaceutical industry up to $740 million per year (source for data) due to false reject rates that can range from 1 to 45 percent, depending on product complexity. In addition to the costs associated with re-inspections, false reject rates can lead to delayed product releases and missed market opportunities.